NASTT Abstract: In 2019, the Weber Basin Water Conservancy District installed the first tight-fit HDPE pipeline liner system inside a large diameter watermain in the state of Utah. The project included rehabilitation of 1.5 miles of 30-inch and 27-inch diameter AWWA C303 “Bar-wrapped” and non-standard non-cylinder reinforced concrete drinking water pressure pipeline originally installed in 1955. The design basis was carried out utilizing a “partially deteriorated” host pipe condition for the majority of the alignment with a fully-deteriorated liner design in select locations based on findings of hydraulic modeling and CCTV observations.
Pressures in excess of 100 psi, steep slopes greater than 40 percent through a valley, and a narrow corridor within an established residential community were part of the construction challenges. Based on the engineering design constraints, the pipeline rehabilitation technologies considered for extending the useful life of the East Layton pipeline included sliplining, cured-in place pipe (CIPP) and tight-fit HDPE lining.
While multiple sliplining materials were considered, HDPE was a preferable material given the need for a more flexible liner to accommodate the topography and presence of rolling terrain. Ultimately the reduction in hydraulic capacity of 20% to 22% that would result from sliplining was determined to be less preferential to other renewal options.
Various CIPP approaches were considered including steam, hot water inversion and UV-cured. The pipeline operating pressures and steep slopes were found to be at or beyond the upper threshold for most conventional steam and hot-water inversion cured technologies considered for the large diameter pipeline. UV-cured CIPP was considered to be the most promising of the CIPP approaches for meeting the pressure requirements of the pipeline; however, the presence of leaking and pulled joints of the host pipe, as well as the rolling terrain exceeding the acceptable deflection angle and made this a less preferred approach than the selected alternative.
Tight-fit HDPE lining was ultimately selected based on the flexibility to meet the operating pressure requirements of the system, improved hydraulic profile over sliplining, and ability to span the existing leaking and pulled joints of the host pipe. For the purposes of this project, Jacobs Engineering selected a semi-structural compressed fit liner system that was intended to stop water infiltration resulting from joint separation without greatly impacting the flow capacity of the existing pipeline.
Successful rehabilitation of the watermain was accomplished through careful collaboration between Owner, Engineer and Construction team. Custom proofing pigs were fabricated to detect and grind joint defects, and a highly successful community relations campaign was implemented for stakeholders along the alignment.
This paper will discuss the planning, installation, and testing of the liner from the perspectives of the engineering team and specialty pipe liner installation contractor (Aegion) with emphasis on engineering considerations during construction, and challenges encountered during installation, and lessons learned. This case study is intended to be a useful reference for pipeline designers, city asset managers, and contractors considering similar large diameter pressure pipeline rehabilitation projects.
Click here to view a recording of the NASTT No Dig Presentation
To purchase the full version of this case study from NASTT, please click on the below link:
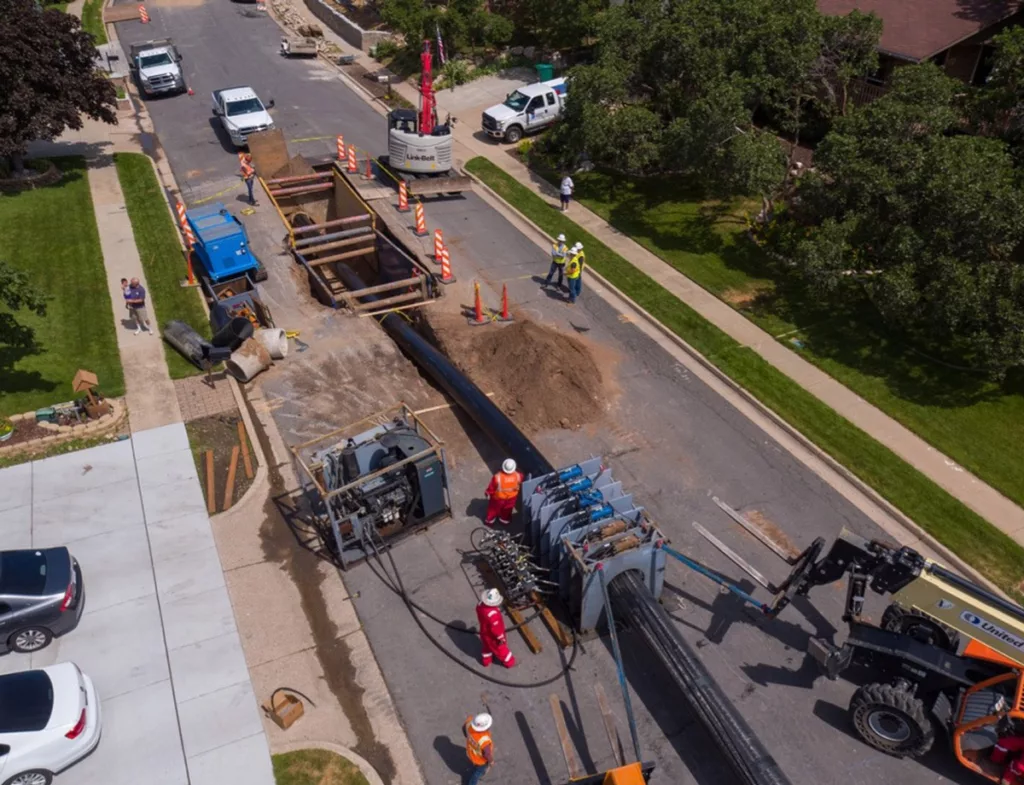