Cured In Place Pipe (CIPP)
Trenchless technology Overview
Cured in Place Pipe (CIPP) involves pulling a resin-saturated liner through an existing host pipe and inverting, expanding, and curing the liner using water, steam, or ultraviolet (UV) light. It can be used to rehabilitate pipelines ranging in size from 2 inches to 120 inches in diameter, in lengths in excess of 1,200 LF between insertion points and can also be pulled through bends or sweeps in the host pipe. CIPP is amongst the most common type of trenchless rehabilitation solutions and has been in existence for over 50 years.
CIPP lining is a great trenchless pipeline rehabilitation solution for gravity applications like sanitary sewer, storm sewers & culverts. It can be used to line a wide variety of host pipe materials including cast iron, ductile iron, concrete, vitrified clay pipe (VCP), wood, etc. Reinforced CIPP can also be used in pressure pipe applications like water and sewer force mains. The epoxy resin-saturated felt tube is relatively thin walled and is often able to maintain the flow capacity of the existing pipeline.
Prior to the installation, the system requires that the existing pipe be completely cleared of blockages and cleaned, but bonding to the host pipe wall is not necessary and the CIPP can be designed to be fully structural with no support necessary from the host pipe.
Another benefit to CIPP liners are the minimal access requirements. Since the epoxy resin-saturated felt tube is flexible prior to the curing process, the trenchless technology system can be installed at convenient locations like manholes or other existing appurtenances.
The felt tube can be impregnated or ‘wet-out’ with epoxy resin onsite or in a close proximity to project location and delivered via refrigerated trucks. Depending on product manufacture, the epoxy can take several hours to cure in ambient conditions, a few hours using steam, or minutes using ultraviolet (UV) light. The liner can be pulled inside the host pipe with a rope tethered to a winch or inverted with air or water.
In summary, CIPP is a great trenchless rehabilitation solution if maintaining flow capacity is a concern and the pipeline alignment has bends or fittings that cannot be accessed and need to be lined.
Gravity Cured In Place Pipe (Gravity CIPP)

Gravity CIPP Capabilities
- Diameter Range: 2″ – 120″
- Maximum Installation Length: 1,200 LF
- Maximum Temperature: 130deg F
- Pressure Rating: N/A
- Liner Wall Thickness: 0.2″-0.5″
- Direction Changes: 90deg Bends
- Cost: $-$$
- Roughness Coefficient: 150
Gravity CIPP Strengths & Weaknesses
Ability To Be Pulled Through Bends
Thin-Walled
Minimal Insertion Access
Inexpensive w/ Widespread Availability
Speed & Complexity of Installation

Pressure Cured In Place Pipe (Pressure CIPP)
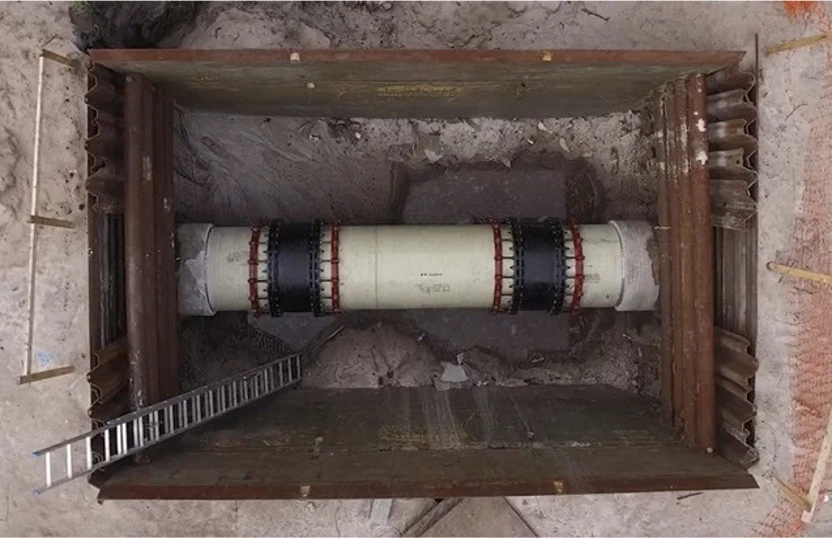
Pressure CIPP Capabilities
- Diameter Range: 6″ – 96″
- Maximum Installation Length: 1,200 LF
- Maximum Temperature: 130deg F
- Pressure Rating: 250psi
- Liner Wall Thickness: 0.2″-1.25″
- Direction Changes: 45deg Bends
- Cost: $$-$$$
- Roughness Coefficient: 150
Pressure CIPP Strengths & Weaknesses
Ability To Be Pulled Through Bends
Thin-Walled
Minimal Insertion Access
Costly
Low pressure Rating Compared to Other Solutions
Speed & Complexity of Installation
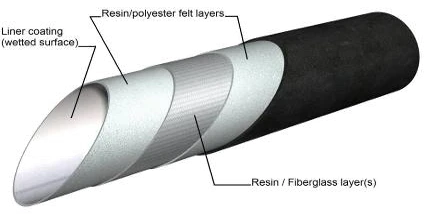
Pipeline Rehabilitation Process:
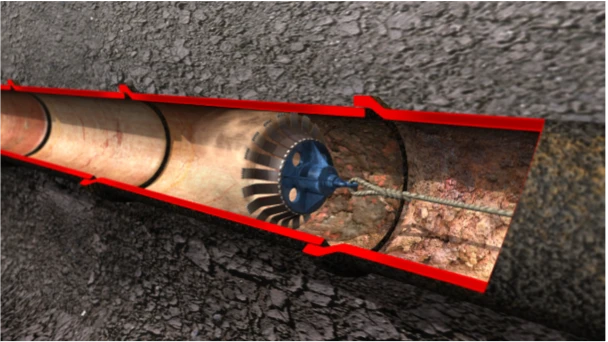
Host Pipe Preparation
Clear blockages, clean and then inspect the condition of the existing host pipe.
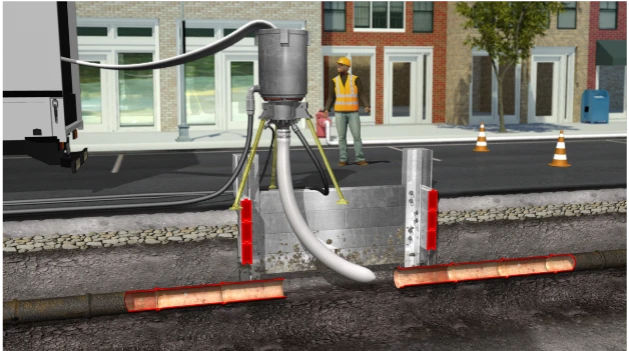
Trenchless Installation
Pull CIPP liner inside of host pipe, pressurize tube and then cure epoxy resins

Terminate Liner & Test
Install end connections and then visually or hydrostatically test integrity of liner