NASTT Case Study Abstract: In 2017, a CO2 pipeline in southern Mexico was in need of an internal trenchless lining solution that would require an innovative new connection method to rehabilitate the pipeline. A pair of CO2 transport carbon steel pipelines owned and operated by Miller Pipeline had been out of service for 22 years and needed to be placed back into service. Miller selected a tight fit HDPE lining system which was then terminated with a custom connection that did not require the use of flanges. A fiber-reinforced polymer (FRP) material was used to externally wrap the connections along with areas of the pipe that required spot repairs.
After an integrity assessment of the host piping was conducted, it was determined the steel pipelines were not fit for service in their current condition. A careful analysis of options gave the owner two alternatives – spend two years building a new pipeline system or rehabilitate the existing system utilizing a trenchless solution. A tight fit trenchless HDPE lining system was selected to rehabilitate the inside of the steel pipeline and stop internal corrosion. The HDPE liner pipe is custom extruded and sized to the internal diameter of the host pipe. During the installation process, the liner is pulled through a reduction die and compressed radially. After the liner has reached the section’s end point; the HDPE will expand naturally and form a tight fit with the inside of the host pipe. This type of trenchless technology could be installed in lengths up to a kilometer without requiring access to the pipeline.
In addition to the tight fit trenchless HDPE lining system, a real-time condition assessment program that provides data collection and can interface with a web-based system to provide a fully-automated cathodic protection system was installed. A FRP system was also used to act as the pipeline’s required CO2 crack arrestors.
By choosing to renovate the infrastructure with the tight fit HDPE lining solution, Aegion was able to commission the pipelines in a matter of months instead of years, spending half the investment required to build new pipelines while reducing right-of-way and construction risks. This paper will detail the project, selection of the solution method and implementation of the multi-component project.
To purchase the full version of this case study from NASTT, please click on the below link:
CO2 Pipeline in Mexico uses New Connection Method with tight fit HDPE liner system
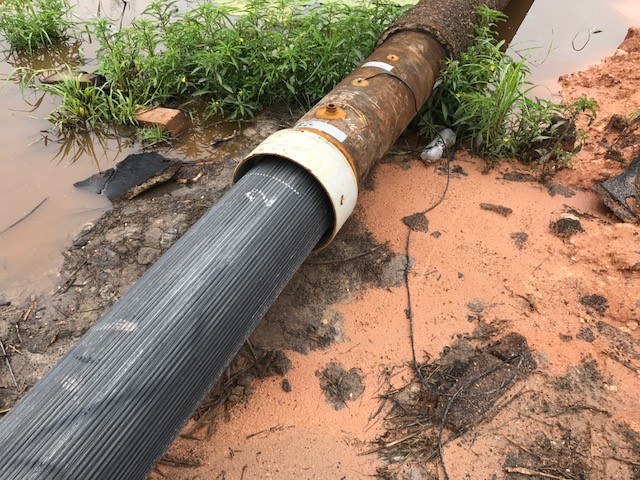
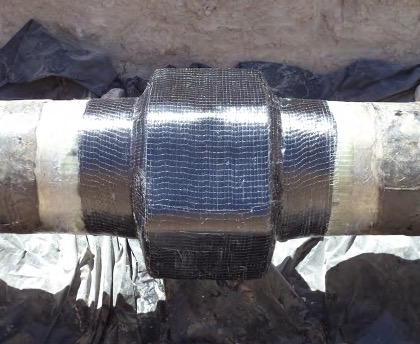