American Society of Civil Engineers (ASCE) Abstract: Trenchless rehabilitation of existing pipelines is a continually growing industry with many viable technologies available to the end user. Pipeline rehabilitation via sliplining methods is a well established means of trenchless construction that can sometimes be overlooked when evaluating rehabilitation options. With many older water and wastewater pipelines now surrounded by adjacent utilities or located beneath ever busier roadways, sliplining offers a low-dig replacement solution that reduces construction risk and minimizes disruption to the public. Difficulties with accessing congested utility corridors via open-cut construction, combined with escalating restoration expenses, make sliplining a cost effective and environmentally attractive design alternative to direct bury replacement.
Sliplining rehabilitation involves installing a new pipe inside an existing pipe, typically by means of pulling a fused thermoplastic material as the new replacement pipe. Trenchless sliplining can be classified into two categories: conventional loose-fit and tight-fit.
The process of conventional loose-fit sliplining is not much more complicated than its name suggests. When an existing pipe is identified as a possible candidate for sliplining, it is an industry best practice to inspect the existing pipe in order to determine its inside diameter and confirm that it is free from obstructions. Once the engineer has an understanding of the existing pipe’s dimensions, they proceed to evaluate materials and sizes for the new pipe to be installed. Sliplining is possible with a variety of materials, but this paper will primarily consider butt-fused thermoplastic piping options due to their prevalence in sliplining applications. These two thermoplastic materials are fusible polyvinyl chloride piping (FPVCP) and high density polyethylene (HDPE) piping
With loose-fit sliplining, the pipe is pulled into place with a small percentage of annular space between the new pipe and the existing pipe. This small amount of annular space helps the new pipe navigate minor joint offsets and deflections in the existing pipe. A variety of equipment options can be used for the installation of FPVC or HDPE piping via sliplining methods. Often times the pipe is pulled with a winch, directional drilling rig, or pipe bursting machine. For shorter runs of less than 1,000 feet, some contractors are able to push the new pipe into the existing pipe by means of “stroking” it with a nylon strap attached to an excavator. When the pipe is pulled into place, it is possible under ideal conditions to achieve continuous pull lengths of several thousand feet and longer.
Once the pipe is pulled or pushed into place, the best practice is to grout the annular space between the new pipe and the existing pipe. The recommended grout to be used for this process is a low density, low strength, cellular grout that can be pumped into the annular space. After the annular space is grouted, the newly sliplined pipe is connected to the rest of the system using standard fittings or fused adapters, depending on whether FPVC or HDPE is the material used for sliplining, respectively.
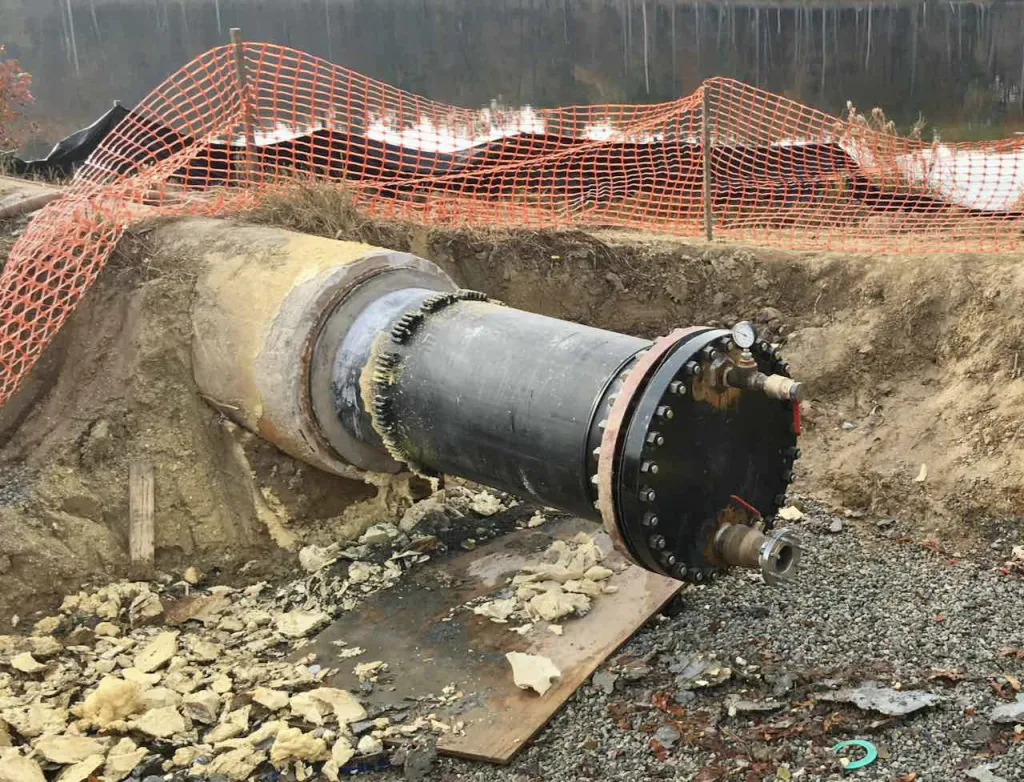
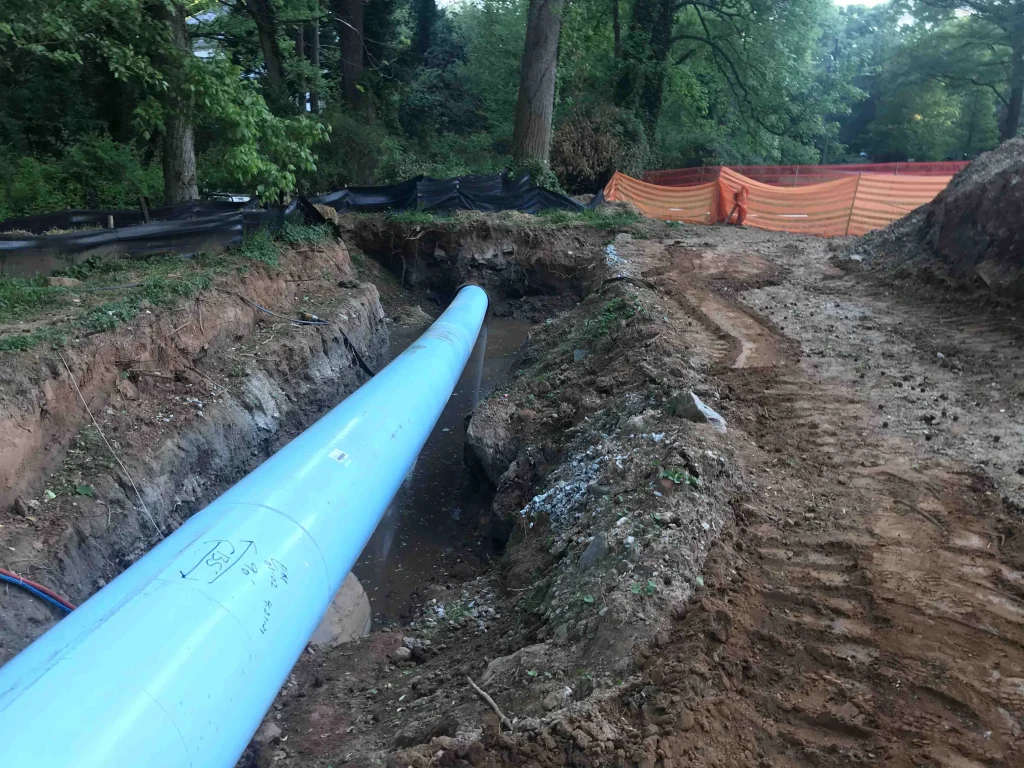
Tight-fit sliplining, sometimes called swage lining or compressed fit HDPE lining, employs many of the same concepts as loose-fit sliplining, but it involves a unique process, which allows the liner to fit tightly next to the existing pipe. In order to install a product that fits tight against the existing host pipe, the tight-fit sliplining process utilizes tooling designed to temporarily compress and reduce the outside diameter of the new HDPE piping to be installed. The outside diameter of the piping is reduced by pulling it through a series of reducing rollers or a reducing die. Once the pipe’s outside diameter has been reduced, it is pulled through the existing pipe with a cable and winch before the material has time to relax and expand back to its normal size. Similar to loose-fit sliplining, the tight-fit sliplining installations can be pulled in lengths over several thousand feet depending on the project specific conditions.
After the new piping is pulled into place, the material is allowed to relax and it expands to fit snugly against the existing pipe. The annular space between the new pipe and the existing pipe is eliminated at the end of the relaxation time. Either flanged or mechanical connections are then fused onto the ends of the HDPE piping to make reconnections to the existing piping.
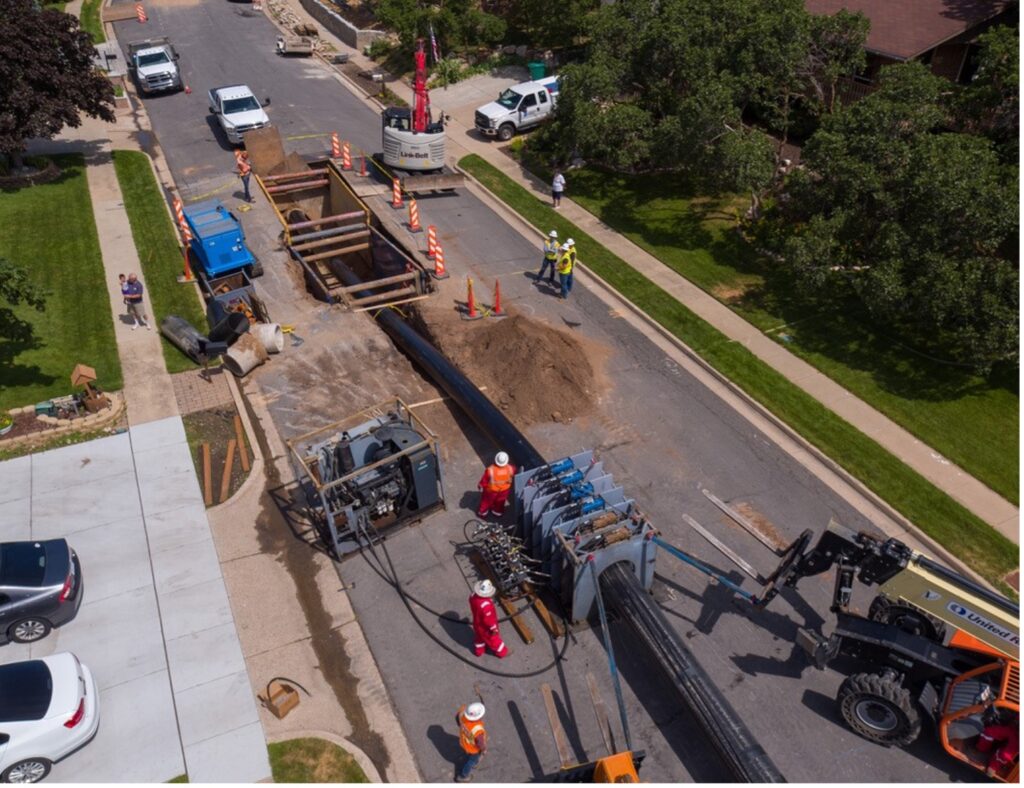