Pipe Lining for the Oil & Gas Industry
When faced with deteriorating or damaged pipes in the oil and gas industry, relining the pipes is a cost-effective and efficient solution that offers a lifespan comparable to a new installation. Companies should consider pipe lining as a viable alternative to pipe replacement for several reasons, and Gemini can help guide your oil and gas pipe lining project.
Pipe lining is the cost-effective and efficient repiping solution for oil and gas companies – extending the lifespan of existing pipes and minimizing service disruptions.
Oil and gas companies should consider pipe lining instead of pipe replacement for several reasons:
Cost Savings
Pipe lining generally offers significant cost savings compared to complete pipe replacement. The cost of excavation, removal, and replacement of pipelines can be substantial, considering the extensive network of pipelines in the oil and gas industry. Pipe lining eliminates the need for such costly and time-consuming processes, resulting in substantial cost savings for your company.
Improved Pipeline Integrity
Pipe lining reinforces and strengthens the existing pipeline, improving its integrity and resistance to corrosion, leaks, and other forms of damage. The lining material can provide enhanced resistance to chemical corrosion and abrasion, improving the durability of the pipeline system. This enhanced integrity helps maintain reliable and safe operations for your company.
Minimal Production Disruption
Pipe lining allows for in-place rehabilitation of pipelines, minimizing disruptions to oil and gas production operations. Traditional pipe replacement often involves shutting down production, rerouting pipelines, and potentially interrupting supply. In contrast, pipe lining can be performed with minimal disruption, enabling continuous production and reducing revenue losses.
Compliance with Regulatory Requirements
Pipe lining can help oil and gas companies meet regulatory requirements for pipeline integrity management. By proactively addressing pipeline issues through lining, companies can demonstrate their commitment to compliance with safety and environmental regulations. This reduces the risk of penalties and ensures the company’s operations align with industry standards.
Shorter Project Timelines
Pipe lining projects typically have shorter implementation timelines compared to pipe replacement. This expedited process allows oil and gas companies to quickly address pipeline integrity issues and resume operations more rapidly. With shorter project durations, the company can optimize productivity and reduce potential revenue losses associated with extended downtime.
Technological Advancements
The field of pipe lining has seen significant technological advancements in recent years, providing innovative solutions for oil and gas companies. Advanced lining materials, such as epoxy-based or cured-in-place liners, offer improved performance, durability, and resistance to harsh operating conditions. These advancements allow companies to benefit from the latest technologies and materials in pipeline rehabilitation.
Extended Asset Lifespan
Pipe lining can extend the lifespan of existing pipelines. By applying a new lining, the integrity of the pipes is restored, preventing further deterioration and minimizing the risk of leaks or failures. This extends the useful life of the pipelines, avoiding the need for extensive replacements and providing long-term cost savings for the company.
Expertise and Industry Support
Pipe lining projects often require specialized expertise and industry support. Numerous companies and professionals specialize in pipeline rehabilitation and offer comprehensive services tailored to the oil and gas industry. Partnering with experienced experts ensures that the pipe lining process is performed efficiently, accurately, and in compliance with industry standards. Gemini can vet contractors and guide you to qualified contractors with specific expertise in your project needs.
Lessen Environmental Impact
Pipe lining offers environmental benefits compared to pipe replacement. It reduces the amount of construction waste generated from excavation and pipe disposal, minimizing the impact on landfills and reducing resource consumption. Additionally, pipe lining reduces the disturbance to natural habitats and ecosystems, promoting environmental stewardship.
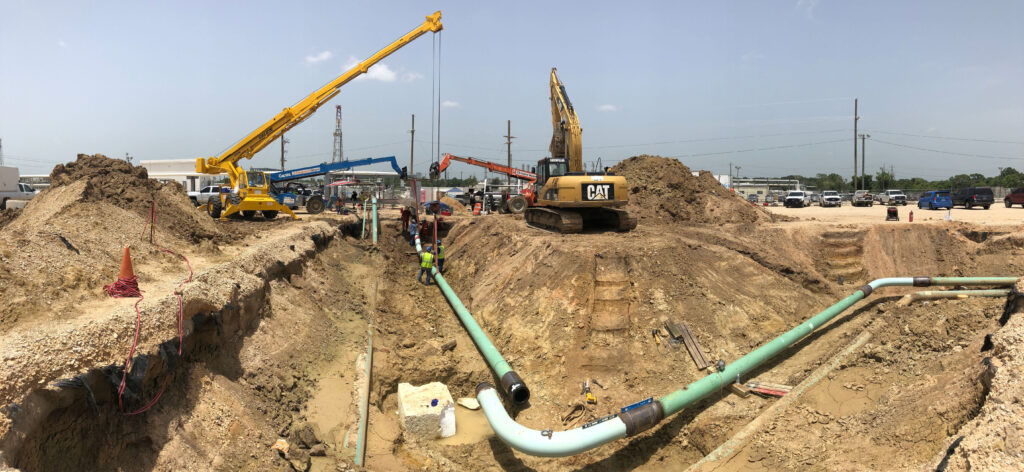
Considering these advantages, pipe lining provides oil and gas companies with a cost-effective, environmentally friendly, and minimally disruptive solution for maintaining and rehabilitating their pipeline infrastructure. By choosing pipe lining instead of pipe replacement, companies can optimize production, extend the life of their assets, and ensure the integrity of their pipeline systems while minimizing costs and operational disruptions.
If your company is planning an expensive pipe project, there are several important factors to consider:
Fluid Compatibility: Determine the compatibility of the lining product with the fluids being transported through the pipes. Oil and gas companies deal with a wide range of fluids, including crude oil, natural gas, and various chemicals. Ensure that the lining product is resistant to the specific chemicals and corrosive substances present in the fluid to maintain pipeline integrity and prevent leakage or degradation.
Installation Method and Equipment: Evaluate the installation method and equipment required for the lining product. Some lining systems may necessitate specialized equipment or specific installation techniques. Consider the availability of the required equipment and the expertise of the installation team. Choose a lining product that aligns with the available resources and capabilities of the oil and gas company or its contractors.
Temperature and Pressure Ratings: Evaluate the temperature and pressure ratings of the lining product. Oil and gas pipelines often operate under high temperatures and pressures. Verify that the chosen lining product can withstand the expected temperature and pressure conditions without compromising its structural integrity or performance.
Chemical Resistance: Determine the chemical resistance properties of the lining product. Oil and gas pipelines may come into contact with various chemicals, including corrosive substances or additives. Verify that the chosen lining product is resistant to these chemicals to ensure its long-term performance and to mitigate the risk of corrosion or chemical degradation.
Pipeline Diameter and Configuration: Consider the diameter and configuration of the pipelines. Different lining products may have limitations in terms of pipe diameter or may require specific conditions for installation, such as straight sections or smooth interiors. Ensure that the chosen lining product can be effectively installed in the target pipelines, considering their diameter and configuration.
Performance Testing and Research: Review performance testing and research data related to the lining product. Look for independent studies, field trials, or case studies that demonstrate the effectiveness and durability of the lining material in oil and gas applications. Consider the product’s track record and any evidence of successful implementation in similar pipeline projects.
Abrasion and Wear Resistance: Assess the abrasion and wear resistance properties of the lining product. Oil and gas pipelines can be subject to abrasive materials, such as sand, sediment, or corrosive particles. Choose a lining product that offers sufficient resistance to abrasion and wear to maintain the longevity and integrity of the pipeline.
Manufacturer Reputation and Support: Assess the reputation and experience of the manufacturer or supplier of the lining product. Research the manufacturer’s history, customer feedback, and references to gauge their reliability and support. A reputable manufacturer with a proven track record can provide ongoing support, technical expertise, and assistance throughout the project and the lifecycle of the pipeline.
Regulatory Compliance: Ensure that the selected lining product complies with relevant industry standards, codes, and regulations. Oil and gas pipelines are subject to stringent regulations regarding safety, integrity, and environmental protection. Verify if the lining product meets these regulatory requirements to ensure compliance and minimize potential risks.
Cost and Value: Evaluate the cost-effectiveness and value for money of the lining product. Consider the initial installation costs, as well as long-term maintenance and lifecycle costs. Compare the pricing of different lining products and weigh them against their performance, longevity, and overall value provided to the oil and gas company.